Titanium metal will play an increasingly important role in the future (especially in the aviation industry) due to its own material properties. Titanium metal has the characteristics of high strength, good toughness, low thermal conductivity and special corrosion resistance. As carbon fiber (CFU) is widely used as aerospace component material, the application of titanium metal parts has also increased. This is because when titanium metal is used in conjunction with CFK, the electrochemical potential difference between the two is greater than that of lead metal and CFK. The potential difference between should be low. In the future, there will be more and larger structural components made of titanium, which puts forward requirements for the design of cutting processing, and it is necessary to provide efficient milling tools that can adapt to titanium processing.
In order to improve the efficiency of milling processing, in addition to the design of the tool's macro-geometric structure, changing the design parameters of its micro-geometric structure is also one of the ways. Here, we must first mention the cutting edge passivation process that plays an important role in improving cutting efficiency. According to people's current understanding, when machining titanium metal, the use of sharp-edged tools is beneficial to improve cutting efficiency. The test results introduced below show that although titanium has such material properties, it can also improve cutting efficiency by appropriately changing the design parameters of the tool's micro-geometric structure.
Cutting edge passivation technology with high reproducibility
The passivation of the cutting edge of the tool usually uses brush, shot peening, barrel polishing, etc. This article introduces a relatively new cutting edge passivation treatment-magnetic precision dressing technology. The two magnetic heads are filled with a scraping medium mixed with magnetic particles. The two magnetic heads rotate at different speeds. The processed tool is placed between the two magnetic heads and rotates in the fluid filled with the scraping medium. The cutting edge, back, front and groove are flushed. This method can also be used to process PVD coated tools.
Since the geometry of the cutting edge of the tool is not completely symmetrical, the degree of passivation is also uneven. In order to clearly describe the geometric structure of any cutting edge, the following parameters are used: the front segment Sγ, the back segment Sα, the segment ratio K, and the radius spacing △r. Previous studies have shown that the passivation of the cutting edge has a great impact on the cutting efficiency of the tool. After further research at present, it is found that the cutting performance of the cutting tool after asymmetric uniform passivation treatment is better than that of symmetric uniform passivation.
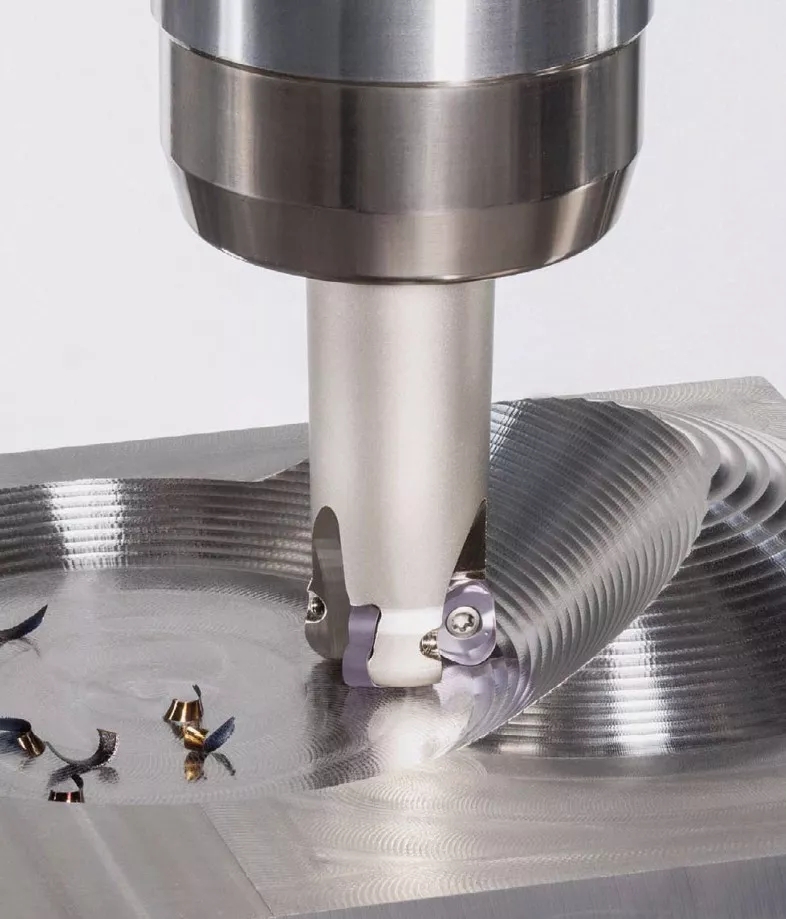
The service life of cutting tools with passivated cutting edges can be increased by 70% when processed according to traditional cutting parameters. The greater the amount of cutting edge passivation, the better the wear resistance of the tool. When cutting tools without passivation treatment, the cutting edge part will appear large wear due to slight damage, and this phenomenon rarely occurs on tools that have undergone passivation treatment. This is because in the cutting process , There will be a lot of pressure on the cutting edge, and some adhesives will be formed on the passivated cutting edge, so that the cutting edge becomes stronger and not easy to wear.
After the tool is passivated, the cutting performance of the cutting edge is more stable, which is particularly important for improving the processing efficiency of titanium. Because the cutting edge damage can be effectively avoided, the distribution and process of tool wear are very uniform and stable, and the safety and reliability of cutting processing are also greatly improved.
In the case of the largest amount of cutting edge dullness, the test data of increasing the feed per tooth shows that when the feed per tooth fz=0.06mm, that is, the durability of the tool is doubled compared to the ordinary cutting conditions The highest degree. The test was interrupted when the cutting amount reached vw=2300cm3. As the cutting stroke of each cutting edge is reduced, the tool durability is greatly improved when fz=0.06mm than when fz=0.03mm.
In order to process the same amount of material, it is necessary to reduce the speed of the tool. When the cutting thickness is greater than the segment Sα behind the cutting edge of the tool, the tool wear can also be improved. However, continuing to increase the tooth feed rate will increase the mechanical load of the machine tool, resulting in increased wear and reduced cutting capacity. In addition, the passivation of the cutting edge can also reduce the chatter generated during the cutting process. Even if higher cutting parameters are selected for cutting, the durability of the tool can still be guaranteed.
After the cutting edge is passivated, the tool wears very evenly during use. At this time, adhesives will be formed on the front and back of the tool.
When the feed rate is large, there is no obvious damage to the cutting edge. For further testing, the feed per tooth is increased to fz=0.15mm, and the depth of cut is reduced to ap=5mm. When the cutting depth is large, the cutting force increases correspondingly, resulting in tool breakage. When the feed rate is also large and the cutting depth ap=16mm, chattering will occur during the cutting process, which will damage the tool and the spindle of the machine tool.
summary
Edge passivation treatment has a great influence on tool wear and cutting efficiency. Circular cutting edges and rotationally symmetrical tools such as milling cutters can be dulled by magnetic precision trimming technology. The front, back and groove of the tool are also polished at the same time, which is very beneficial to avoid adhesion. When a tool with a passivated edge is used to mill titanium according to traditional cutting parameters, its durability can be increased by about 70%, and the feed per tooth can also be significantly increased. The test shows that when the feed per tooth fz=0.06mm, the cutting state of the tool is the best, and no slight damage is observed on the cutting edge of the tool.